Stay ahead in nondestructive testing with ASNT's live webinars, designed to provide solutions and insights from industry experts. Earn contact hours while gaining practical knowledge that directly applies to your work in NDT.
View Upcoming WebinarsBrowse Webinar Archives)
ASNT Conferences and Events
Connect with industry leaders, enhance your expertise, and advance your career at ASNT's top events and conferences for NDT professionals.
Upcoming Events
ASNT Members get Event Benefits
Did you know that Professional and Pro Plus members get discounted pricing on registration for ASNT events, conferences, and webinars?
Get more value from your event experiences.
Learn More About Membership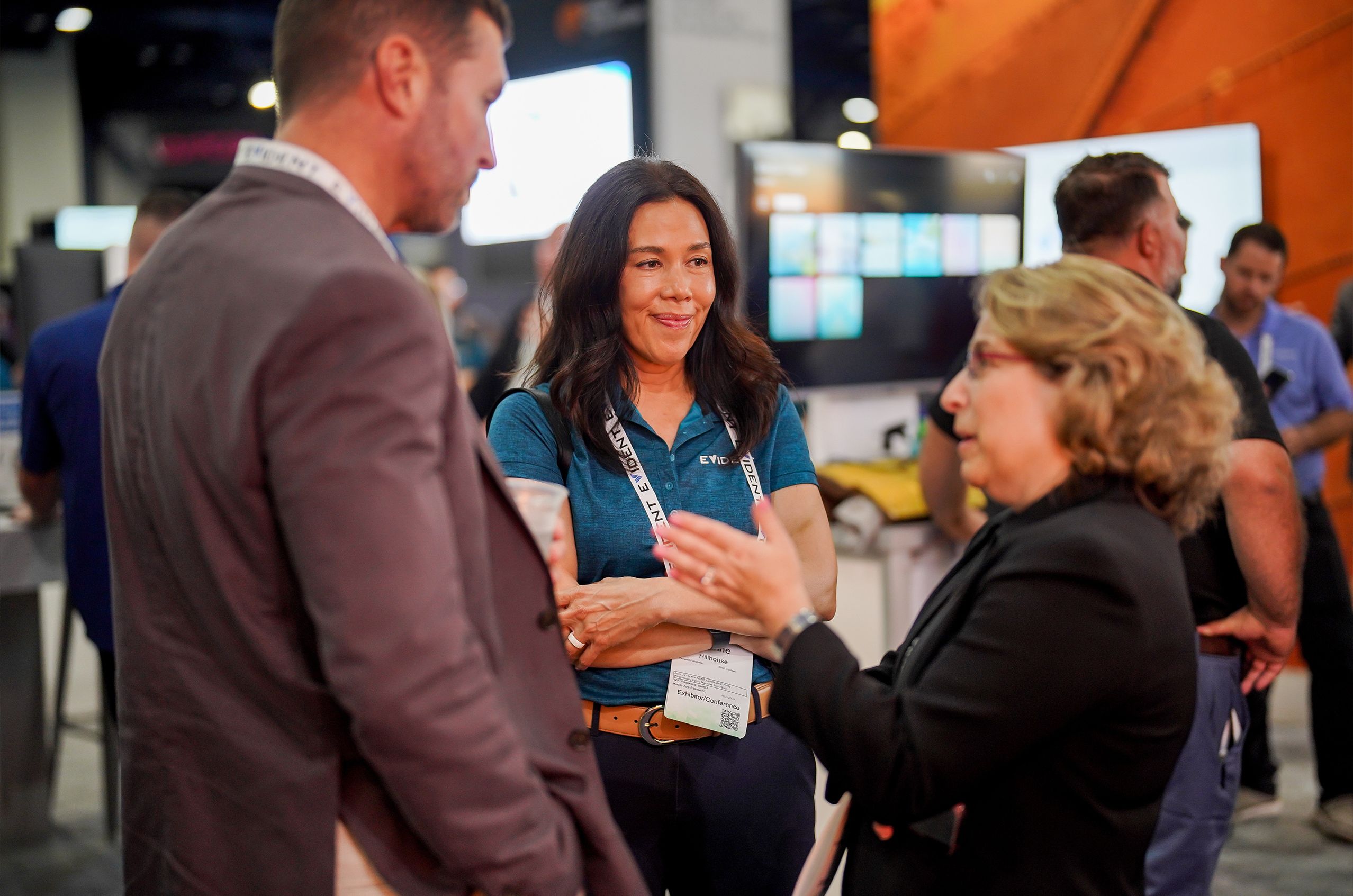
Frequently Asked Questions
Level III recertification points are offered at all ASNT conferences and vary for each event.
The process will vary based on the event. For conference technical sessions, an email will be sent after the event with instructions. Webinars and short courses are entered by staff based on attendance.
The cancellation policy will vary by event. Typically, a registered attendee may cancel at any time, up to 30 days prior to the event, and incur, at most, a $100 cancellation fee. A registration may be transferred to another person, at any time, with no cancellation fee.
To cancel or transfer your event registration, contact customer support at customersupport@asnt.org or by calling 614-274-6003.
Generally, a citizen of a foreign country who wishes to enter the United States must first obtain a visa. Visitor visas are nonimmigrant visas for persons who want to enter the United States temporarily for business (visa category B-1), tourism, pleasure or visiting (visa category B-2), or a combination of both purposes (B-1/B-2).
Attending a scientific, educational, professional, or business convention or conference falls under the category of B-1.
There are several steps to apply for a visa. We encourage you to begin that process. Please visit U.S. Department of State — Bureau of Consular Affairs to learn more about applying for a visa.
Event specific information for exhibiting at an ASNT event can be found on the Exhibit and Sponsor tabs of each event's website.
This is best handled by contacting customer support at customersupport@asnt.org or by calling 614-274-6003.